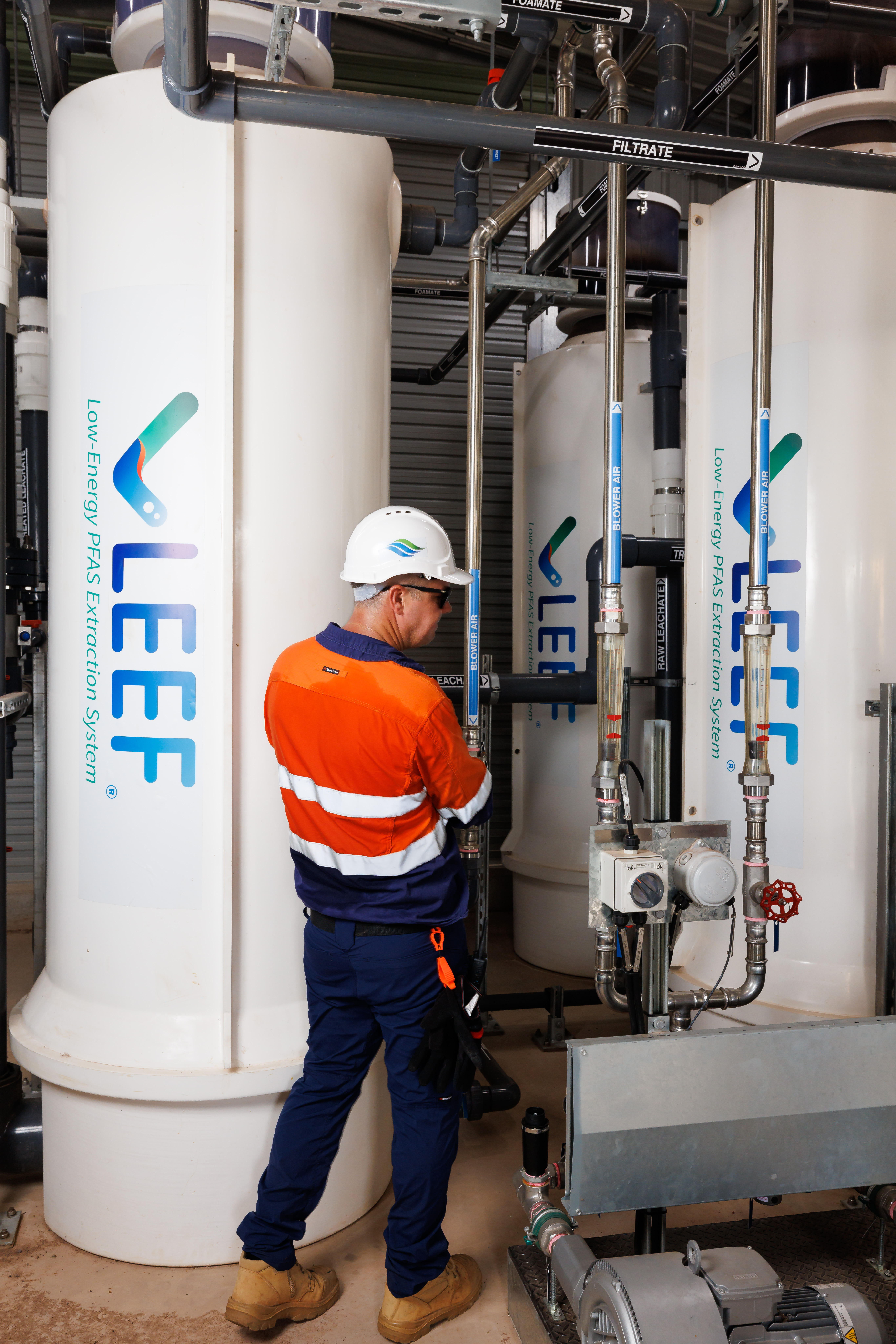
LEEF system recognised for PFAS removal
25 August, 2023
An Australian developed foam fractionation system for PFAS removal is gaining global recognition in leachate treatment.
A ban on PFAS use is the only way to eliminate per– and polyfluoroalkyl substances (PFAS) contamination.
But you’d have to strip back the manufacturing process of many everyday products, from baking paper, non-stick cookware to cosmetics, carpets, and clothing, that it’s too big of an ask, says Mark Mullett, PFAS and Mining Development Manager for the Water & Carbon Group (WCG).
He says there are no official discussions around trying to reduce the amount of PFAS that consumers use, but it’s a hot topic among waste and recycling operators who are left with the financial impost of cleaning up the forever chemical.
Landfill operators are often challenged by treating and managing PFAS in leachate and groundwater. One of the main difficulties is the complex chemistry of the leachate – high salinity, organic carbon, non-biologically degradable compounds, suspended solids, and nitrogen compounds, particularly ammonia, are present.
“There are a lot of PFAS removal technologies available that all have their sweet spots in terms of the feedwater source chemistry,” Mark says, “but it’s very hard to find a solution to treat all of them.
“No single process can be developed for just any leachate. Even within a single landfill site, the leachate sources are sufficiently different to require their own assessment and process development.”
Granular activated carbon (GAC) absorption and ion exchange resins have been used to treat PFAS in simple waste streams.
Mark says membrane processes such as reverse osmosis (RO) can be applied to leachate treatment, but the volume of concentrated waste produced is high, 20-50 per cent of the raw leachate volume, resulting in high waste disposal and energy costs.
This is even more apparent when the RO concentrate is further treated using high energy evaporation processes to drive the excess water off as steam.
WCG has developed the LEEF (Low Energy Evaporative Fractionation) System to remove PFAS contaminants by harnessing air, and the chemical properties of PFAS itself, while using minimal energy, and no consumables.
PFAS are surfactants that can produce a stable foam when mixed with air and water. This characteristic is the reason PFAS is effective as a firefighting foam to suppress certain types of fire.
The LEEF System has worked on some of the most challenging chemistries found in leachate.
The LEEF System takes advantage of the way PFAS coats air bubbles in a process called foam fractionation. By adding air in a controlled setting, PFAS compounds will attach to bubbles and rise to the top where they can be skimmed off and separated.
Mark says the LEEF System has worked on some of the most challenging chemistries he’s seen in leachate.
“The LEEF System is not impacted by the co-contaminants and is quite robust to suspended solids,” he says. “It’s why foam fractionation in general is being considered the primary treatment option for leachate.”
The LEEF System is in full operation at the Shoal Bay Leachate Treatment Plant in Darwin, where it is successfully treating 50 million litres of leachate each year as part of a holistic zero liquid discharge leachate treatment regime.
It’s also had success in treating about a dozen of the toughest leachates in US states including Tennessee, Vermont, Alabama, North Carolina, and Virginia in demonstration and pilot scale trials. The demonstration plant uses full-sized commercial fractionators to treat more than 12,000 litres per day in continued operation.
Mark says the level of demonstration has given clients confidence in the LEEF process and many are taking a proactive approach to implement solutions that best suit their situation. That’s been spurred on by a US Environmental Protection Agency proposal for nationally enforceable limits for six PFAS compounds that are commonly found in drinking water. The regulation will require various industries, including landfill operators and those involved in leachate management, to proactively prepare for compliance in advance.
WCG is also receiving requests for treating water from mining run-off, groundwater influenced by hydrocarbons, and landfill sources that carry industrial waste, not putrescible household waste.
“These are quite problematic in their own way for traditional treatment that are compromised by the background chemistry,” Mark says. “In some cases, very complex pre-treatment is required to accommodate the traditional removal technologies to eradicate contaminants.
“Each of these pre-treatment stages can produce its own PFAS contaminated waste. In these instances, the LEEF System has many advantages including operational efficiency and being cost-effective, and sustainable.”
The Water & Carbon Group continues to invest in a development program at bench and pilot scale to refine and improve operations, and to develop operating parameters for more feed source types.
Mark says Australia’s proactive approach to PFAS – the government recognized PFAS as a potential problem far earlier than some other countries and has developed a nationally agreed guidance on the management of PFAS contamination in the environment – has resulted in many innovations, such as the LEEF process, originating in Australia.
“Australia has always been on the ball with PFAS and is a pioneer in terms of solutions development,” he says.
“To see these being exported, along with enhanced technical knowledge in terms of understanding PFAS and PFAS abatement, is very exciting.”
This article originally appeared in Waste Management Review here, authored by Lisa Korycki.